こんにちは、品質管理ドットコムの山本です。国立大学で修士号を取得し、現在は東証一部上場企業の品質部門にて活躍しています。私の情熱は「品質」にあり、製品品質の評価と品質管理を専門としています。
今回は「5Sとは」と題して記事を書かせていただきます。
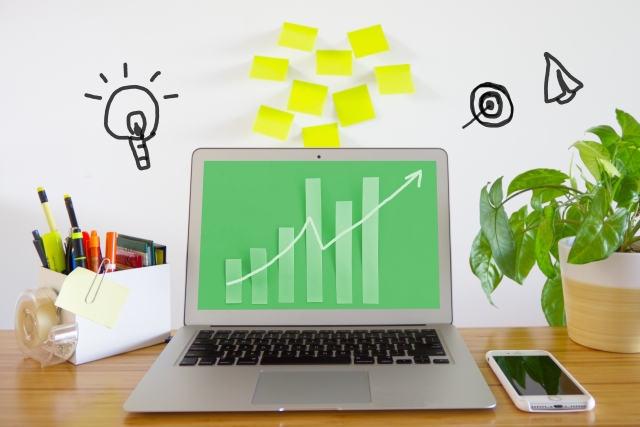
前書き
製造業における5Sは、効率性や品質向上、安全性確保などにおいて重要です。整理・整頓・清掃・清潔・躾の5つの原則を実践することで、作業環境を改善し、無駄を削減し、作業効率を向上させることができます。また、整理整頓により、作業者が必要な物をすぐに見つけられる状態を維持し、安全な職場環境を促進します。これにより、生産性や品質向上、事故やミスの防止など、企業の競争力向上に貢献します。
5Sとは?
5Sとは、整理(Seiri)、整頓(Seiton)、清掃(Seisou)、清潔(Seiketsu)、躾(Shitsuke)の頭文字をとった言葉です。これらの行動を実践することで、職場や作業環境を整え、効率的かつ安全な状態に保ちます。整理・整頓・清掃が具体的な行動を示し、清潔・躾はその状態を維持するための意識を表します。徹底的な5S活動により、品質や生産性を向上させることが可能です。
5S活動を行う目的
職場環境を整えることは、作業効率や作業品質に直結します。徹底的な5S活動は、単に綺麗な職場を維持するだけでなく、効果的な生産性向上や品質保証にも貢献します。結果として、職場環境が整頓されたり、清潔な状態が維持されることで、作業効率が向上し、従業員の安全性も確保されます。
(1)作業効率が向上する
整理・整頓・清掃が行き届いた職場では、物の配置が明確になっており、「必要なものがすぐ手に入る」状態です。これにより、作業者が時間を「探す」のではなく、「実際に作業する」ことに費やせるため、作業効率が向上します。
さらに、作業スペースの配置やアクセスのしやすさも最適化され、物理的な作業効率も向上します。
(2)より安全な職場になる
整理・整頓・清掃が行き届いている職場は、「物が散乱していない」環境です。このような環境では、作業者が物にぶつかったり、つまづいたりするリスクが軽減されます。
5S活動の継続的な実施により、転倒や衝突などの事故リスクを低減し、職場の安全性が向上します。
(3)従業員の満足度が向上する
整理・整頓・清掃の徹底は、働く環境を快適にし、従業員の満足度を高めます。整頓された職場は、作業しやすく、過ごしやすい環境を提供します。
このような働きやすい環境は、従業員の満足度を向上させ、活気ある職場文化の醸成につながります。
(4)ルールを守る風土を作る
5S活動は一人だけの努力では成立しません。細かなルールの遵守は、全員が参加することで成り立ちます。これにより、整頓された職場環境が維持され、作業効率が向上します。
ルール遵守の意識は、職場内だけでなく、他の場面でも活かされる重要な資質です。
3.5S活動がうまく進まない!上手な推進のヒントは?
実際に5Sを導入してみたものの、うまくいかなかった経験はありませんか?特に中小企業では、活動に時間を割く余裕がなく、「作ったけれども形骸化してしまった」ということもあるでしょう。
5Sが失敗する主な原因を4つ挙げてみました。
- 社員の積極性が足りない
- 時間に追われて継続できなかった
- 5Sの必要性が伝わっていない
- ルールが定まっていない
(1)社員の積極性が足りない
5S活動が上手く進まない一因は、社員の積極性不足です。通常業務に加えて整理整頓を行うことは、労力が必要です。従業員の多くは、これを「余分な仕事」と捉えがちです。したがって、上位職が率先して取り組むことが不可欠です。部下や後輩に対してルールを押し付けるのではなく、自らの行動で示すことが重要です。また、5S活動委員を配置することで、組織全体に浸透させることができます。
(2)時間が不足して継続できなかった
5S活動は継続が肝心です。定期的に時間を割いて行うことが必要です。具体的な計画を立てて、整理整頓の対象や方法を明確にすることが重要です。また、単に決まりを作るだけではなく、会社全体で取り組む姿勢が大切です。
(3)5Sの重要性の認識が不足
従業員に5S活動の重要性が伝わっていないため、「5Sの必要性」について理解していない社員が多いかもしれません。
職場での事故や労災を詳しく分析すると、「5Sが不十分であった」ことが事態を悪化させたケースもあります。
もちろん、生産性の向上やルールの遵守も重要ですが、最も重要なのは「従業員の安全」です。5Sを継続的に行うことで、安全で働きやすい環境を維持します。
そのためには、過去の事故や他社の事例を挙げて、従業員に教育する時間を確保する必要があります。
新入社員研修はもちろん、定期的なトレーニングや社内のe-learningシステムを通じて教育を繰り返すことが必要です。
(4)ルールの不明確さ
最後に挙げるのが、「5S活動を推進する!」と意気込むものの、具体的なルールが定まっていないため、従業員は「何をすれば良いのか?」と迷うこともあるかもしれません。
職場環境ごとに「何を、いつ、どのように行うか」を明確にするルール作りが重要です。事務所、製造ライン、倉庫など、それぞれの環境に合わせてルールを定めることが必要です。
以下に、それぞれの環境におけるルール化の具体例を示します。
《事務所でのルール化の例》
- 書類を年度ごとにファイリングする。
- 書類を収納する棚には年度が書かれたラベルを貼る。
- PCや他の電子機器の電源コードを整理して、歩きやすい環境を保つ。
《製造ラインでのルール化の例》
- 使用する治具の配置場所を決める。
- 摩耗品の廃棄場所を指定する。
- 不良品の一時保管場所を決める。
《倉庫でのルール化の例》
- 在庫の置き場所を決めて、カラーテープで識別する。
- 台車の置き場所を決める。
- フォークリフトの走行ルートを指定し、物が置かれないようにする。
まとめ
今回は、5Sという考え方の基本から、具体的な組織の問題や継続するメリットについてお話ししました。5Sとは、整理、整頓、清掃、清潔、躾の頭文字を取った言葉です。これを実践することで、作業効率が上がったり、安全な職場が作られたり、従業員の満足度が向上したり、ルールを守る風土が醸成されます。5Sをただ形式的に行うのではなく、全ての従業員が積極的に取り組み、その重要性を理解し、計画やルールをしっかりと構築することが大切です。
「もっと詳しい情報が知りたい」や、「こんな情報教えて欲しい」ということがありましたら、お気軽にご連絡ください。
最後までお読みいただきありがとうございました。興味があれば、他の記事もご覧ください。