こんにちは、品質管理ドットコムの山本です。国立大学で修士号を取得し、現在は東証一部上場企業の品質部門にて活躍しています。私の情熱は「品質」にあり、製品品質の評価と品質管理を専門としています。
今回は「工程管理とは」と題して記事を書かせていただきます。
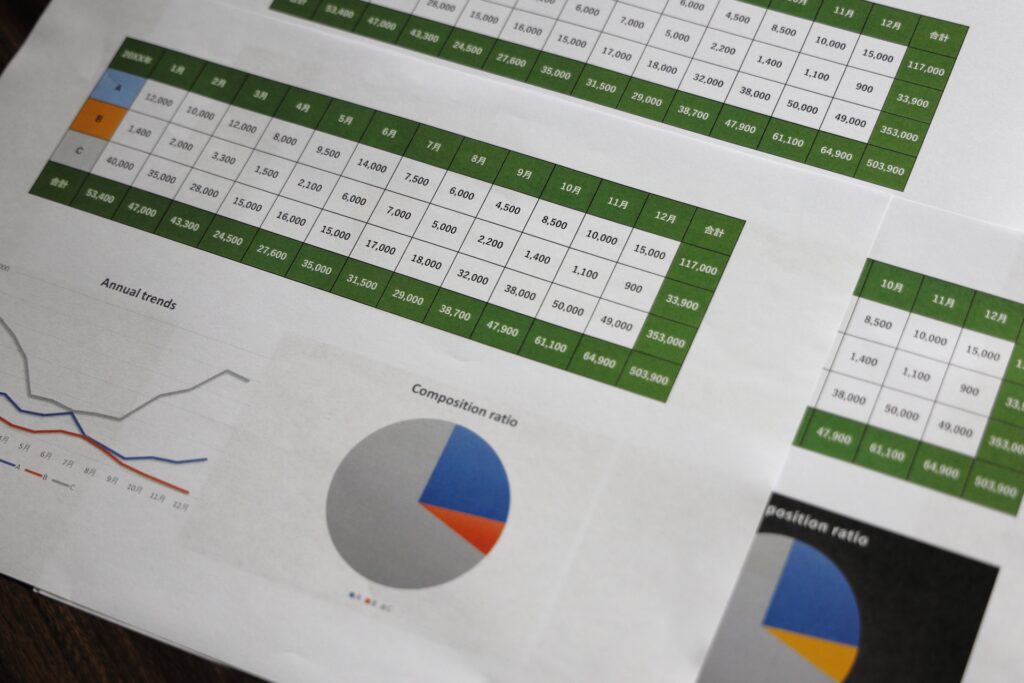
前書き
工程管理は、製造プロセスやプロジェクトの各段階を計画し、調整することで効率性や品質を確保する管理手法です。工程管理では、作業手順の設計、リソースの配分、スケジュールの管理、品質の監視などが含まれます。これにより、生産ラインやプロジェクト全体を効率的に運営し、納期遅延や品質低下などの問題を最小限に抑えます。
この記事では、製造業における工程管理の重要性についてご紹介します。
工程管理とは?
「工程管理」とは、通常製造業で使われる言葉で、生産の手順を合理的にコントロールし、必要な人員や設備、材料などを効果的に調整することです。製造部門だけでなく、営業や開発などの部門でも業務の進行をスムーズにするために用いられます。
「工程」とは本来「作業の段階」を指します。プロジェクトを計画する際、適切な工程管理が欠かせず、そのため、プロセス管理は生産に限らずその他のプロジェクトでも必要です。
工程管理と生産管理の違い
「工程管理」と「生産管理」は似ていますが、いくつかの違いがあります。
生産管理は製品の全体的なフローを管理し、材料調達、製造、出荷、売上追跡、品質管理などを含みます。長期的な視点で製品の全体的な管理を行います。
一方、工程管理は製造プロセスに焦点を当て、具体的には製造ステップや段階の進行に重点を置いて管理し、納期を守り、製造プロセスがスムーズに進行し、適切な進捗があるかを確認します。つまり、工程管理は生産管理の一部と言えます。
工程管理の目的
工程管理には様々な目的がありますが、主に以下の4つが製造現場にもたらされます。
締め切りの順守
製造現場では、納期を厳守することが最優先事項です。そのためには、常に在庫や資材、人員などのリソースを把握しておくことが不可欠です。
工程管理を適切に行うことで、工程の進捗を計画的に把握するだけでなく、材料不足や人員欠員などの突発的な状況にも備えることができます。
生産効率の最適化
「生産性向上」と「コスト削減」は製造現場の永遠の課題です。しかし、製造状況を可視化できなければ、改善案の立案や実施は難しいです。工程管理を実施することで、製造状況を可視化し、生産効率の向上に向けた施策を講じることが可能です。
品質の確保
生産量の増加に伴う品質のバラツキは深刻な問題です。工程管理を導入することで、必要なリソースを把握し、バッファを設けることで品質の向上につながります。
製造原価の削減
製造プロセスの効率化により、生産原価やその他のコストを削減できます。さらに、必要な原材料の種類と量を把握することで、在庫リスクを軽減し、保管コストも削減できます。
従来の工程管理手法と最新のシステム
従来の工程管理手法は主に「紙」「ホワイトボード」、または「Excel」を使用していました。これらの手法にはそれぞれ長所と短所があります。
紙・ホワイトボード
利点
工程の進捗を即座に目視できるため、情報の共有と更新が容易です。また、必要なのは紙とペンだけであるため、コストも低く抑えられます。
欠点
作業者が現場にいない場合、情報の更新が難しいため、リアルタイムでの共有には適していません。
Excel
利点
Excelを使用することで、複雑な情報をわかりやすく可視化できます。また、マクロを活用することで手動入力を自動化できる利点もあります。
欠点
編集権限が一人に限定されるため、共有性に課題があります。
工程管理システム
これらのことから、最近の現場ではシステムが導入されているところが少なくありません。これにより、変更点を迅速に共有できます。しかし、選択するシステムは自社の製造現場のニーズとシステムの特性を十分に考慮する必要があります。
工程管理システムについては、さまざまな企業が紹介していますので、それらの中から現場にあったものを選ぶようにしてください。
まとめ
工程管理とは?ということで簡単に解説を行いました。現場で起きるトラブルというのは多種多様なことがありますので、管理しているからといって100%防げるものではありません。ですが、日々の管理を行うことで、トラブルを未然に防ぐという考え方が大事になってきます。
「もっと詳しい情報が知りたい」や、「こんな情報教えて欲しい」ということがありましたら、お気軽にご連絡ください。
最後までお読みいただきありがとうございました。興味があれば、他の記事もご覧ください。